The Complete Guide to
Underfloor Air Distribution
Key Elements and Common Mistakes When Implementing UFAD
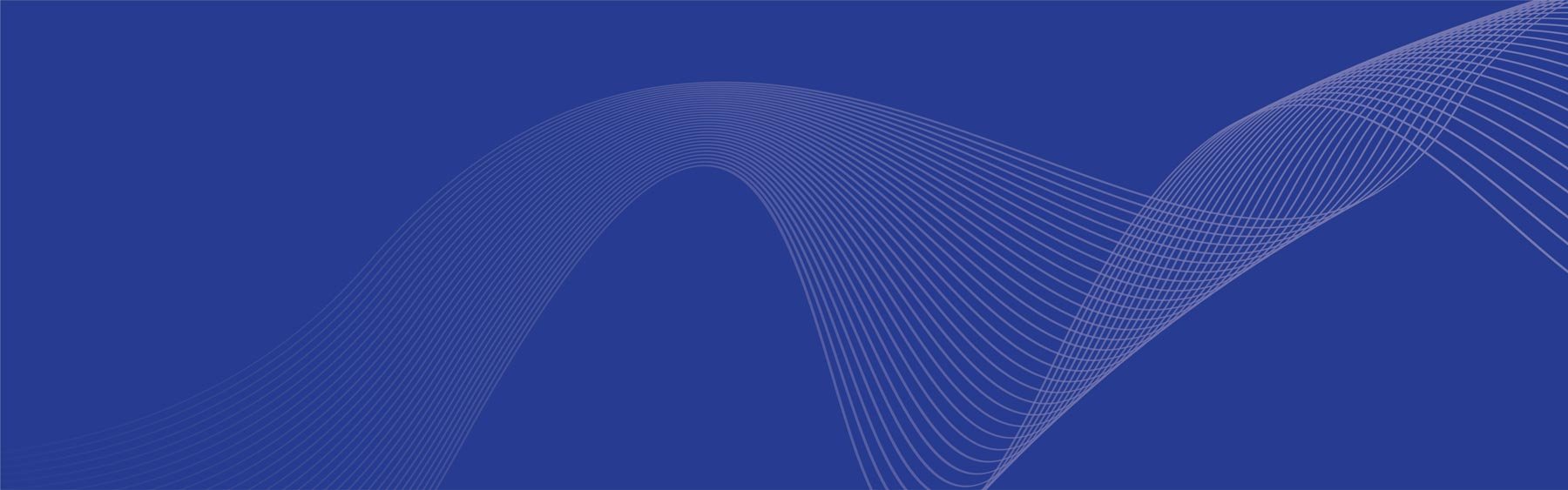
Underfloor Air Distribution
Installing an underfloorfloor air distribution system is a major investment for any organization. But more often than not, the project will pay for itself.
When designed with care and implemented properly, UFAD offers incredible return on investment through:
- Improved employee productivity and health
- Increased occupant comfort
- Reduced operating (energy) costs
However, when laid out poorly or installed carelessly, a UFAD system can be a drain on your resources.
Improper setup can result in delayed start-up, occupant discomfort, and inflated energy costs — potentially leading to expensive repairs… or even a complete overhaul.
To help you avoid all these issues, we’ve put together the complete guide to underfloor air distribution.
Designing the Supply of Air Distribution
Contrary to popular belief, buildings don’t require an “even” amount of heating or cooling throughout.
You can’t just dump supply air into the plenum space of a large building floor plate and expect that to result in even temperatures across the facility.
Areas that have increased heat concentration, such as perimeter zones, need extra cooling to maintain a consistent desirable temperature. Conversely, very low load areas such as hallways, storage rooms and unoccupied meeting rooms require limited plenum air. Air needs to be carefully delivered in a way that the entire building has a consistent temperature level, at a set point that enhances worker productivity.
Perimeter Zones
The outside areas of buildings — closest to the outdoor environment — usually have increased heating and cooling requirements. Areas with direct sunlight, exposure to windows, and those near entrances are the main culprits. These areas of high cooling load concentration need to be supplied with the coolest underfloor supply air.
Interior zones have better comfort when supply air is 3-5 degrees warmer than that.
So, unsurprisingly, careful planning is needed to ensure effective supply air temperature levels throughout the facility.
For example, installing small sheet metal ducts operating (by design) at relatively high velocity, will allow them to distribute the cool supply air to zones furthest from the central air handling units. But these ducts need to be small enough to fit between support pedestals of raised access floors.
The problem?
In the past, engineers have designed UFAD ductwork based on their experience with overhead ducting. Overhead duct systems can create objectionable noise at duct velocities above 1500ft/min. Further, overhead ducts are installed in a ceiling plenum where 24, 36, 54 inch widths are not a big issue. But these principals DO NOT apply to ducting under the floor.
Ducts need to be 22 inches wide and 1-2 inches shorter than the space under the floor.
The concrete filled, steel reinforced, floor tile provides significantly more sound blockage and attenuation than a ceiling tile. Additionally, high discharge velocities out of UFAD ducts are needed to minimize air temperature rise.
Thus, it is good design practice to use higher duct velocities (about 2500 ft/min on a design day at 100% flow) with UFAD systems. If ducts under the floor “need” to be wider than 22 inches, it is better to use multiple ducts sized to fit between the raised floor pedestals.
Return Air Paths
The path for return air is one of the most important aspects to consider when designing a low pressure supply air plenum system.
Unfortunately, many designers will either completely overlook this aspect, or pay it little mind — ultimately resulting in poor system design.
A properly designed return air path will create more efficient warm return air flow back to the AHU, maximizing comfort and reducing costs in the long run.
Return Air Design for Underfloor Air Distribution
Overhead systems typically utilize duct pressures of .25 to 2 inches water column (“wc). Those systems are seldom concerned with return air pressure drop.
If overhead systems have a return air pressure restriction, the room might become pressurized, but comfort will mostly be maintained.
This isn’t so for an underfloor system, where supply pressure tend to be very low: .05”wc (12.5pa).
While this is the industry standard (and is generally good for plenum leakage and fan efficiency), it necessitates a free flowing, low pressure drop return path.
Care must be taken to see that return air velocities in perimeter zones are 100ft/min through the return grille free area. Internal areas closest to the central air handler should be sized for 200ft/min.
If the ceiling plenum is continuous, a very small negative pressure can be expected if you follow the above guidelines. But if the ceiling that the AHU pulls through is not a continuous plenum (like in a “cloud” decorative ceiling), there will be no negative pressure in the ceiling plenum. So allowances must be made to pressurize rooms to expel warm return air.
Over-sizing supply diffusers to deliver design flows at .03”wc (allowing room pressure of .02”wc) is one method.
If the return path is severely restricted, fan boosted systems might be required; however, this can usually be avoided.
Wall Construction
There are two primary reasons that bad wall construction can occur:
The first is a result of inappropriate design or construction of the wall itself.
Underfloor plenums must be air-tight; and some designers don’t fully take this into account. As a result, they neglect to properly seal any intrusions, cracks, or holes.
The second main cause of poor wall construction is based on the misconception that walls must extend below the raised access floor “for acoustic purposes” — a perception that is factually incorrect.
If the walls around an office are built to the floor slab, the short section of wall under the floor is almost never the path of least resistance for sound. So unless the wall construction is STC -50 or higher, this underfloor wall does not improve the acoustics of the room.
Extending a wall under the floor has several notable negative effects:
- It blocks supply air, along with all wiring and piping access (the main reason for the raised floor in the first place!)
- The project is more expensive because it requires additional panel cuts.
- The wall will end up having many penetrations, completely neutralizing any possible acoustic benefit
Inappropriate Wall Design
The golden rule of working with underfloor air distribution is this:
If you make a hole, you seal that darn hole. Not next week. Not later. Right then and there.
And this applies to walls as well.
Poorly designed walls can often have cracks, which compromises the integrity of your plenum. Careful inspection of walls is required at each step of construction to ensure no cracks, holes, or other intrusions remain.
Acoustic Walls
Offices and other facilities will often opt to add walls to maintain good acoustics or visual appeal. All walls should be placed on top of the raised access floor unless it’s an exterior wall, core wall, wet wall, or demising wall.
Designing & Supervising your UFAD Plenum Construction
The integrity of your plenum is integral to the long-term health of your UFAD system.
A well-designed and implemented plenum will have all cracks sealed, with controlled airflows and limited blockage.
Sealing Cracks
When installing a UFAD plenum system, a good rule of thumb is that if one creates a hole, the same trade needs to make sure it’s sealed with plenum-safe caulk as soon as they’re done. You’ll also need to ensure that the bottom of all columns are sealed to prevent upward airflow.
Uncontrolled Airflows
The efficiency of your UFAD system’s plenum can be sabotaged by uncontrolled airflows. Air entering walls and/or the return air system, or exiting the building in an uncontrolled way results in significant losses in efficiency through “Category 1” leakage. “Category 2” leakage results from uncontrolled air entering the interior occupied space from the plenum. While this is considered more like minimum airflow, and not really leakage, too much (30%+) can result in overcooling the occupied space.
In any case, extra attention and effort is critical in ensuring air tight plenum integrity.
Construction Sequence of Raised Access Flooring
Once a UFAD system has been designed and the construction process has begun, there are many critical steps that must be completed in a specific order. Otherwise, your UFAD system may not properly function… if at all.
Throughout construction, inspection and sealing are two important processes to keep in mind. This applies both before and after completion of the installation of raised access flooring.
Before Installation of RAF
Once you’ve cleaned the area and begun to lay down components, you’ll need to do a considerable amount of sealing. Every seam, hole, and penetration of any kind needs to be closed to enable the plenum to function properly.
At every step in the process, you should inspect components to make sure they’ve been properly installed.
After Installation of RAF
Check for gaps around the edges of the floors. You may need to use caulking on joints to ensure the enclosure is properly sealed. As before, if you’ve created a hole or penetration of any kind, make sure it’s sealed IMMEDIATELY. More experienced contractors use colored caulk (not clear, grey or white) because it is so much easier to see what you are doing. Quality control of the plenum sealing can be done at a glance.
During this process, you’ll want to inspect each element of the system, from thermostats to floor panels to the diffusers.
Priorities
Installing a UFAD system can seem expensive.
But trying to cut upfront costs during installation can lead to poor comfort and diminished productivity from people using the facilities.
For businesses, this can mean thousands of dollars of lost productivity. In the case of some commercial HVAC systems that are in buildings such as casinos, bad systems can result in diminished customer comfort, decreased retention, and ultimately, lost revenue.
As such, it’s crucial to consider the negative life cycle cost impact of value engineered (VE) proposals or other cost reductions.
A common mistake, in our view, is to install manually controlled systems in lieu of modern thermostatically controlled variable air volume (VAV) systems.
The diffuser and its controls are the “User Interface” of the air conditioning system, and even the best central systems will go to waste if the “final mile” of the air distribution and control is not done correctly.
Seldom is the premium for a VAV system more than $1 per square foot, and in return it will offer the most consistent and comfortable environment for the people working in the space.
Anything that is done that negatively effects comfort will have a productivity penalty for the life of the building. Save $1 per sq.ft. one time; lose $5 per year in productivity forever.
Heat Load Calculations
A building’s air conditioning tons are the same, as are all the AHU casing and coil sizes — although the airflow might be a bit different (+ or – 15%).
That’s why we believe that the best way to estimate loads is to run the cooling load based on your experience with overhead VAV systems and local knowledge.
Using that as a starting point, we would make small adjustments to adapt the calculation for a UFAD system. There are several different factors that need to be accounted for during the estimation of a given space’s heating load, and can be grouped into two main categories:
- Internal loads (people, lights, and relatively minor electronic devices)
- Skin loads (solar-based heat, glass transmissions, and wall transmissions).
Internal Loads
During the design process, you need to factor in all people, small power loads, and a portion of the lighting load into the airflow calculation.
A good rule of thumb is that your UFAD system will need to handle 20% of the overhead lighting load. This is because a significant portion of the heat created from overhead lighting occurs over the ceiling, and therefore doesn’t impact the space.
When planning a UFAD system, heat generated by small power or plug loads is only 60-70% delivered to the conditioned zones. While not a significant factor, much of this load rises to the ceiling without mixing into occupied space.
Skin Loads
There are a variety of ways that heat can flow into or out of a building. This includes sunlight entering through windows, warming up the exteriors of buildings (known as solar gains), and the loss of air to the outside environment through leaks and infiltration.
Properly designed and positioned perimeter diffusers can make a notable difference in the effectiveness of these systems. We recommend diffusers to be positioned at the perimeter, aimed inward at an optimal 15° angle to minimize convection on walls or glass and lessen draft on occupants. This strategy will reduce perimeter convection by 35%.
Very high ceiling areas can be calculated considering only the lowest 6-8 feet of occupied volume – a clear advantage of a stratified UFAD system.
Operation of AHU Systems
The sequence of operation for AHU systems refers to the specific order of instructions that your system will go through for each function. This is a commonly mishandled process that could have disastrous consequences if installed incorrectly.
For instance, in the event that you forget to include controls for building pressure, doors can pop open or windows can even break.
These errors occur due to a lack of oversight during design, implementation and installation. Sometimes the engineer’s sequence is poorly written; other times it’s correct but never installed or validated. In either case, the fundamental instructions are not in place for the system to function correctly.
UFAD Diffuser Selection
An integral part of a underfloor air distribution system are the UFAD diffusers that are installed within it.
Each building and space will have different needs that can be, in part, met by a choosing the right kind of diffuser.
There are two primary types of diffusers, both of which with their own sets of uses. Which type you’ll want to use will depend on your building and its occupants, as well as the designer’s aesthetic preference.
Manually Controlled Diffusers
One of the main methods for controlling airflow in interior spaces are a system of manually adjusted floor mounted diffusers. These diffusers are composed of a mixing style diffuser and a volume adjustment method in the face of the grille.
As each of these diffusers are adjustable, occupants are freely able to alter the rate of airflow through their diffusers to a level that makes their space comfortable for them. These floor mounted diffusers are designed to combine the air exiting the plenum system with existing occupied space air within a highly controlled radius and at low velocities.
Most airflows created by these diffusers typically ranges between 30 to 150 CFM per diffuser.
This manual adjustability is nice, but these diffusers don’t control air temperature, shut themselves off when spaces are unoccupied, and they don’t provide any BAS system feedback or interface. Achieving consistent comfort at all changing loads and occupancies is very tricky.
Automatic VAV diffusers
Modern office buildings almost always have automatic thermostatically controlled systems in perimeter zones and conference rooms.
We believe that the BAS automated control strategy should be used in 100% of all UFAD projects.
If one needs to economize, you can compensate by using larger thermostatically controlled zones. This strategy is the most conservative sure-fire way to guarantee a good project and a satisfied owner. No matter what changes – air temperature, local load conditions or occupancy – these systems can adapt.
The thermostat also reports local zone conditions, documenting the correct functionality of the system.
The Cost of Underfloor Air Distribution
One of the primary reasons why some projects don’t provide good return on investment (ROI) is because organizations choose to invest their money in ways that don’t offer returns.
For instance, many designers will push for perfectly flat floors. This is completely unnecessary for the success of a UFAD project and is a waste of resources, as the raised access floor will compensate for an uneven subfloor.
Expensive floor sealing methods are sometimes prescribed, and they too offer no future benefit for occupants.
A recent example of poor investment was a building with AHU’s costing over $10 per square foot, paired with the lowest cost plastic, manual diffusers. The result was poor temperature control in occupied zones, which impacted comfort and productivity.
Roughly $1-1.50 more per square foot would have provided thermostatically controlled VAV to all occupants, dramatically increasing returns on their productivity for the lifetime of the building.
The key to achieving good ROI is to focus on improving the comfort of your occupants. First cost and even energy costs are, overall, a fraction of the cost of worker productivity.
Contact Our UFAD Experts!
Fill out the form today to get more information on how UFAD will help you reduce energy costs and improve air quality.